Manufacturing
Hands On Metal Fabrication at ADX Portland
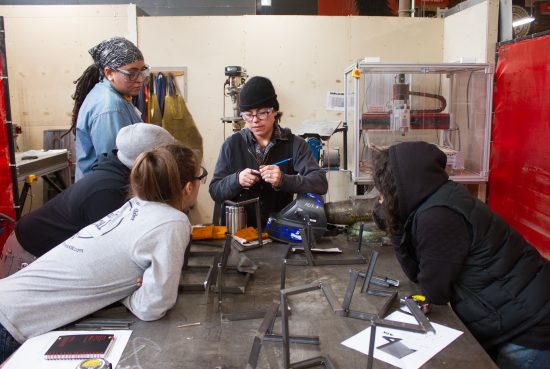
TACC students learning how to assemble their frames
On Thursday, February 8, 2018, Oregon Tradeswomen’s Trades and Apprenticeship Career Class (TACC) had the opportunity to get hands on experience with metal fabrication! Metal fabrication is the altering of raw materials by way of bending, cutting, welding, etc. in order to build structures. This hands on day happened at ADX Portland, a makerspace where people can share tools and knowledge, and take advantage of a huge facility with a wood shop, metal shop, print shop, and jewelry shop.
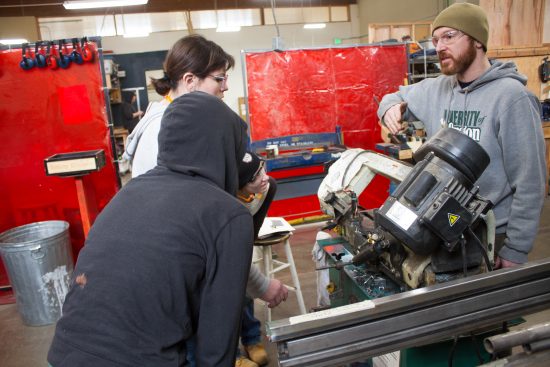
TACC students learning how to operate a Horizontal Band Saw
Our students were tasked with creating their own plaque stands. They were each given 5 sections of channel iron and learned how to cut and grind their materials. They used a horizontal band saw to cut, and a disc grinder to grind down and clean up the edges. Students learned the ever valuable lesson, “measure twice, cut once,” a carpenter’s proverb that also applies to metal fabrication. This rule is important to consider because it is, of course, faster to double check your measurements than cut incorrectly and have to waste time and resources making the cut again.
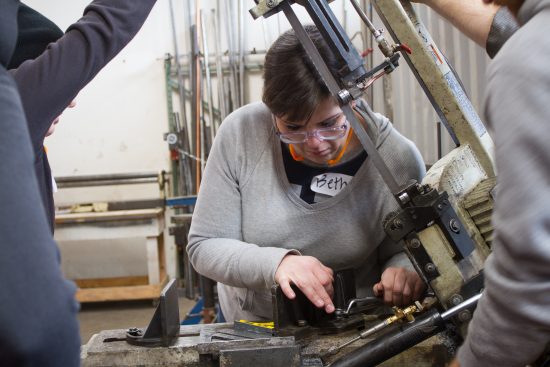
Measure twice, cut once!
Once each of the students prepped their materials, the class learned how to “tack weld” their iron segments together to make a frame. A tack weld is just a series of small welds spaced some distance apart. This type of weld is usually only a temporary step in the welding process, but it holds the assembled components in place and ensures their alignment which is all that is needed for a small project like a plaque stand. After the welds are complete, the students cleaned them up by gently using an angle grinder to smooth out any protruding material.
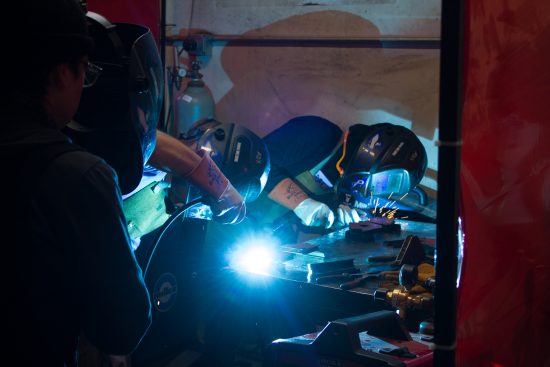
TACC students tacking their segments together
It was clear that our students were enthusiastic about learning to craft with metal and it was an added perk that they got to take home something that they build with their own two hands! Special thanks to ADX for allowing our students to learn about another great option for a career in their beautiful space.
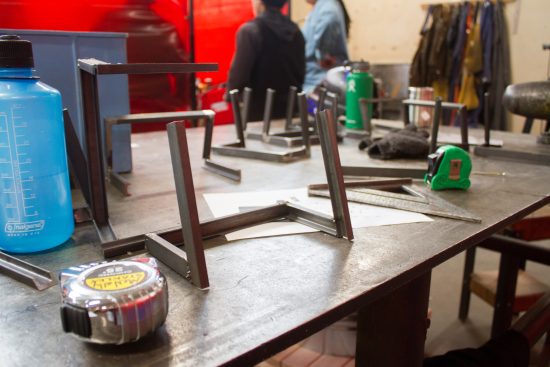
Our students’ final product!
OTI Alumnae Spotlight: Meet Jess Kurtz!
Jess Kurtz grew up in Oakland, California in a low-income neighborhood with an underfunded school system and fewer opportunities. But, Oakland was also a socially conscious community with a deeply embedded awareness for radical activism that made a lasting impact on Jess’s life and sparked a lifelong interest in human rights. Her grit and determination helped her find her way to pursue work that would eventually lead her to land a very lucrative job in corporate marketing with a great salary, but little work-life balance. While in this position, Jess was in a terrible accident and was sent to Portland, OR for reconstructive surgery at OHSU. Following this life changing experience, Jess decided to stay in Portland and leave her 80-90 hour a week career in the corporate world behind in hopes of finding a job that mirrored her passion for women/worker’s rights, and bringing manufacturing jobs back to the United States.
Once settled in Portland, Jess purchased some goats and started a nonprofit now known as the Belmont Goats, which is near and dear to the hearts of many in the Portland community. Jess also held a job as a union negotiator at Communication Workers of America Local 7901 where she met Madelyn Elder, the current CFO at Oregon Tradeswomen Inc. She kept in touch with Madelyn over the years and when she learned about OTI she kept the organization in the back of her mind.
Later, Jess worked at a glass and metal manufacturing facility where she was introduced to welding by a coworker. She fell in love with the trade and enjoyed learning a tangible skill. During this time, Jess was in involved in an abusive relationship with her partner who was also a coworker. When she was assaulted on the job, Jess’s sense of safety in her workplace was compromised. Like many employers, Jess’ did not have the skills or knowledge about how to deal with intimate partner violence in the workplace. Although Jess liked her job and felt a sense of loyalty to her employers, she ultimately chose to leave.
Upon leaving that job and taking some time to heal, Jess was motivated to continue working towards her goal of being a welder and called Madeyn to learn about how OTI could help her. Jess enrolled in OTI’s first Women in Metals and Manufacturing cohort and finished the course with high praise from her instructors and a deeper appreciation for the importance of women in the trade industry. She finished the program in 2015 while also working on finishing up her Associates in Applied Science in Welding Technology at Portland Community College. After taking some time off to travel in Europe, Jess is back in Portland and just accepted a job at Big Marine with hopes of entering the Boiler Maker apprenticeship as soon as possible.
Jess’s future goals include becoming a journeyman welder and a Certified Welding Inspector with the hopes that she can be an independent contractor and work abroad. She would also someday like to have her own welding company so that she can provide a safer workplace for women, people of color, and members of the LGBTQ community. Jess is a champion for the work that OTI does and hopes to be able to give back by being a mentor for other women who want to enter the trades.
When asked what her advice would be for women who are considering a career in the trades she said “entering the trade of your choice by way of an apprenticeship is the most valuable thing you can do in regards to making more money and being a professional in your trade”. She also spoke about the skill of learning how and when to stand up for yourself as a woman in the industry while also learning when to bite your lip and follow orders in order to gain more respect from your peers.
MANUFACTURING ROUNDTABLE EVENT
Overview
The manufacturing industry is projected to need to replace more than 30,000 workers in the next decade, and increasing diversity within the industry is critical to ensure companies have access to the skilled, talented labor required for this important sector of our local economy. Manufacturing in Portland is comprised of more than 107,000 jobs, making up 11% of Portland’s total workforce. In Oregon, overall, 26% of our GDP comes from manufacturing.
On Wednesday, April 22nd, Bank of America and Oregon Tradeswomen, Inc. convened a group of 22 manufacturing industry executives to introduce them to OTI’s forthcoming Women in Metals & Manufacturing program and to learn from them what they are looking for in an entry level worker.
During the 90 minute discussion, OTI learned firsthand from representatives from local manufacturing firms about 4 broad buckets of work to address prior to launching the new Women in Metals & Manufacturing program:
1) Input on the curriculum & framework of this new manufacturing program
2) Ideas about how to recruit for the program, create awareness, and market the program
3) How local manufacturing employers can be a part of the program with things like site visits, guest speakers & hands-on training opportunities,
4) How to facilitate connections to women role-models who are successful in their manufacturing careers
Oregon Tradeswomen also learned more about what skills are necessary for entry level employment in the industry and career advancement, and overwhelmingly, those industry representatives echoed the following skills:
- Mechanical aptitude
- Safety minded
- Ability to learn and apply learning
- Keen attention to detail
- Great attitude / Enthusiastic
- Teamwork Oriented
- Respectful
- Driven
The Structure of the Women in Metals & Manufacturing program:
The Women in Metals & Manufacturing program will consist of two parts:
- A one day, hands-on orientation session which introduces women to metals and manufacturing careers, pathways into these careers, and a hands-on activity designed to allow women to experience activities common in manufacturing jobs in order for participants to assess their level of interest and/or their ability to keep pace with the demands of a manufacturing career.
- A two-week program modeled on Oregon Tradeswomen, Inc.’s nationally recognized
pre-apprenticeship program, Women in Metals & Manufacturing will offer:- Education and training in shop math
- Blueprint reading
- Worksite expectations
- Developing a manufacturing resume
- Hands-on training activities
- Mentoring from women who are successful in a manufacturing career
- Field trips to local manufacturing companies
- Hands-on training in workshop safety and the safe operation of manual/computerized machines and precision tools
- Graduates will receive job placement assistance and vocational case management services upon program completion.
Timeline:
Oregon Tradeswomen, Inc.’s program staff will be distilling the feedback we received at this roundtable to help inform the curriculum of our Women in Metals & Manufacturing program. The new program is slated to launch in August 2015 with an orientation, and then the 2 week intensive training will be offered in early September.
Input Survey:
Oregon Tradeswomen, Inc. welcomes additional feedback from the manufacturing industry to help inform our forthcoming program. If you would like to contribute, please download our survey and return it to:
Dennise M. Kowalczyk
Oregon Tradeswomen, Inc.
3934 NE Martin Luther King, Jr. Blvd., Ste.# 101
Portland OR 97212